When it comes to aluminum machined parts, Davantech stands out as a trusted partner for businesses worldwide. Our advanced CNC machining services deliver precision, speed, and cost-effectiveness, making us the go-to solution for aluminum milling, turning, and custom manufacturing. With a state-of-the-art facility spanning over 2000 square meters and ISO9001:2015 certification, we ensure top-tier quality and reliability for every project.
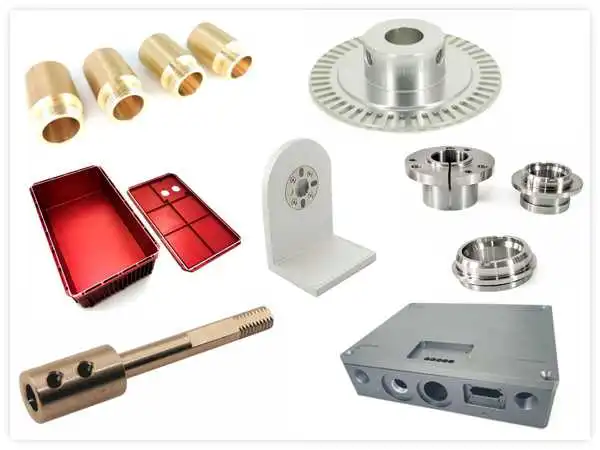
Machined aluminum parts.
Aluminum stands as a perfect choice for industrial components and construction materials. Consequently, CNC machining emerges as a prevalent method for fabricating aluminum parts. Specifically, its commendable thermal conductivity renders it ideal for crafting heatsinks and cooling elements. Moreover, aluminum milling parts exhibit remarkable strength-to-weight ratios, while the metal’s exceptional machinability ensures efficient fabrication processes. The propensity of cutting tools to effortlessly remove chips further enhances aluminum’s appeal, establishing it as the preferred material for a diverse array of milling and turning applications.
To elucidate, CNC-machined aluminum parts encompass electronic enclosures, frame extrusions, LED lighting components, mounting brackets, machinery elements, aircraft components, and a broad range of industrial parts.
Why Choose Aluminum for CNC Machined Parts?
Aluminum is a versatile material widely used in industries such as aerospace, automotive, electronics, and construction. Its unique properties make it ideal for CNC machining:
- Lightweight yet durable: Excellent strength-to-weight ratio.
- Thermal conductivity: Perfect for heatsinks and cooling components.
- Machinability: Easy to machine with high precision and tight tolerances.
- Corrosion resistance: Suitable for harsh environments.
- Recyclable: Environmentally friendly and sustainable.
- Customizable: Available in various grades (e.g., 6061, 7075, 2024) and surface treatments like anodizing, powder coating, and more.
Applications of CNC-Machined Aluminum Parts
Our CNC-machined aluminum components are used in a wide range of industries, including:
- Electronics: Enclosures, heatsinks, and LED lighting parts.
- Aerospace: Aircraft components and structural parts.
- Automotive: Mounting brackets and machinery elements.
- Industrial: Frame extrusions, custom brackets, and precision tools.
Advantages of Davantech’s Aluminum Machining Services
- Expertise in Aluminum CNC Machining:
- Skilled engineers and technicians with extensive experience in aluminum milling and turning.
- Advanced CNC machinery for high precision and efficiency.
- Comprehensive Material Options:
- Wide range of aluminum alloys, including 6061, 7075, 5052, 7050, and more.
- Custom sourcing for specific alloy requirements.
- End-to-End Solutions:
- From design and prototyping to production and surface finishing.
- Additional services like anodizing, powder coating, and wet painting for enhanced durability and aesthetics.
- Quality Assurance:
- ISO9001:2015 certified processes.
- Rigorous quality control at every stage, ensuring compliance with design specifications.
- Cost-Effective Manufacturing:
- Optimized processes to reduce production costs without compromising quality.
- Fast turnaround times for both small and large-scale orders.
Our Aluminum Machining Process
At Davantech, we follow a meticulous process to deliver high-quality aluminum machined parts:
- Design & Planning:
- Detailed CAD models and technical drawings.
- Selection of the right aluminum alloy and machining techniques.
- Material Selection:
- Choose from popular alloys like 6061, 7075, or custom grades.
- CNC Machining Setup:
- Precision calibration of CNC machines.
- Secure workpiece mounting for accurate results.
- Tooling & Cutting Parameters:
- Use of high-performance carbide or HSS tools.
- Optimized cutting speeds and feed rates for efficient material removal.
- Coolant & Lubrication:
- Application of coolants to reduce heat and improve surface finish.
- Machining Operations:
- Roughing and finishing processes to achieve tight tolerances.
- Advanced chip control for smooth operations.
- Quality Control:
- Precision measurement using calipers, micrometers, and CMMs.
- Surface Finishing:
- Optional treatments like sandblasting, polishing, or anodizing.
- Cleaning & Packaging:
- Thorough cleaning and secure packaging for safe delivery.
Custom Surface Finishing Options
Enhance the functionality and appearance of your aluminum machined parts with our custom surface treatments:
- Anodizing: Improves corrosion resistance and adds color options.
- Powder Coating: Durable and customizable finishes.
- Wet Painting: Wide range of colors and textures.
- Polishing & Sandblasting: For a smooth or matte finish.
Range of aluminum materials:
Aluminum 6061, Aluminum 2024, Aluminum 5052, Aluminum 6063, Aluminum 7050,Aluminum 7075, and more. We source any requested aluminum alloy.