Nylon CNC machining shapes materials by removing excess material from a workpiece. In manufacturing, it’s essential for creating parts. PA66 or Nylon is a popular material for machining. This article provides a comprehensive guide.
What is PA66 or Nylon?
Nylon is a synthetic polymer that is widely used in various industries due to its excellent mechanical properties. PA6 and PA66 are thermoplastic materials that are characterized by their high strength, rigidity, and toughness. In addition, it also has good chemical resistance and can withstand high temperatures. Nylon is widely used in the automotive, aerospace, and electronics industries, among others. There are 2 types of Nylon: PA6 and PA6.6. More specific, The impact resistance of PA6 is better than PA6.6 and solubility resistance is also better. On the other hand, PA6 absorbs more water than PA6.6, as a result, it will dehydrate in warm and dry environments and become brittle.
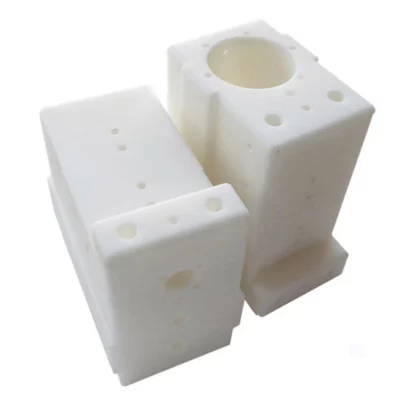
Machining PA66: The Process
Machining PA66 or Nylon requires a good understanding of the material properties and the machining process. The following are the steps involved in machining PA66 or Nylon.
Step 1: Select the Right Tooling
The first step in machining PA66 or Nylon is to select the right tooling. More specific, the tooling used for machining PA66 or Nylon should be made of high-speed steel or carbide. in addition, it should also have a sharp cutting edge and be able to withstand high temperatures. The recommended tool angles for machining PA66 or Nylon are between 10 and 15 degrees.
Step 2: Set the Cutting Parameters
The cutting parameters for machining PA66 or Nylon depend on the material properties and the desired surface finish. To clarify, the recommended cutting speeds for machining PA66 or Nylon are between 200 and 300 feet per minute. Also, the feed rates should be between 0.002 and 0.008 inches per tooth. The depth of cut should be between 0.020 and 0.050 inches.
Step 3: Fixturing
Fixturing is the process of holding the workpiece securely during the machining process. As a matter of fact, the fixturing used for machining PA66 or Nylon should be designed to provide maximum support and stability. The recommended fixturing methods for machining PA66 or Nylon are clamping and vacuum chucking.
Step 4: Machining
The machining process for PA66 or Nylon involves cutting the material to the desired shape and size with a milling or turning machine. The cutting process should be carried out with a constant flow of coolant to reduce the heat generated during machining. In addition, the coolant should be water-soluble and compatible with the material.
Step 5: Finishing
The finishing process for Nylon involves removing any burrs or rough edges on the workpiece. To clarify, the recommended finishing methods for machining PA66 are deburring, sanding, and polishing.
Advantages of Machining PA66
Machining PA66 has several advantages, including:
- High strength: PA66 withstands heavy loads and stresses effectively.
- Chemical resistance: It resists various chemicals, including oils, fuels, and solvents.
- Heat resistance: Nylon maintains its mechanical properties even at high temperatures.
- Easy machinability: PA66 is easily machined using standard equipment.
Applications of Machining Nylon
Typical parts made of Nylon are gears, bushings, cable binders, hinges, etc. Machining PA66 is used in a wide range of applications, including:
Automotive: The Automotive industry uses to manufacture parts such as gears, bearings, and fuel tanks.
Aerospace: The aerospace industry uses PA66 to manufacture parts such as engine components, landing gear, and electrical connectors.
Electronics: The electronics business selects Nylon to manufacture parts such as cable ties, connectors, and switches.
Industrial: The industry in general likes PA66 to manufacture parts such as rollers, gears, and bearings for heavy-duty machinery.
Consumer goods: Manufacturers of consumer goods use Nylon to manufacture parts such as kitchen utensils, sporting equipment, and toys.
Conclusion
Machining PA66 or Nylon is an important process in the manufacturing industry. In other words, it is essential to select the right tooling, cutting parameters, and fixturing methods to ensure a successful machining process. In addition, Nylon offers several advantages, including high strength, chemical resistance, and heat resistance. As a result, the industry uses it widely in various applications, including automotive, aerospace, electronics, industrial, and consumer goods. If you’re in need of machining PA66, be sure to work with an experienced and reputable machining provider to ensure the highest quality plastic parts.