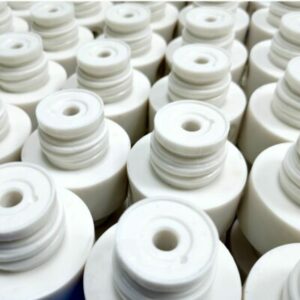
At Davantech we do injection molding of PVDF among a range of raw plastic materials. Next to PVDF, we process ABS, PP, PA66, HDPE, PE, PC, PC-ABS, TPU and TPE. Our injection molding and overmolding activities started back in 2010. More specific, we are a leading mold maker and manufacturer of plastic parts located in China. It has to be said that it is still an obvious choice to have your molds made in China. Because, the manufacturing supply is very broad and efficient. As a result, we offer molds much cheaper compared to Western mold makers. This is a benefit for you. In addition to PVDF injection molding we also manufacture CNC machined PVDF components.
Polyvinylidene Fluoride (PVDF).
We use Polyvinylidene Fluoride for multiple applications across the industry. For example, there are many products in the chemical process industry, wire and cable industry, semiconductor industry and oil and gas industry. In addition, PVDF also gains share in automotive, building, electronics, pharmaceutical and batteries.
We process PVDF easily under a variety of conventional thermoplastic molding techniques. Therefore, the material is particularly suitable for injection molding and extrusion. PVDF is inherently pure and has a good chemically resistance against a variety of aggressive fluids and solvents.
The material has excellent dimensional stability, abrasion resistance and high strength. And above all, it maintains its mechanical properties at elevated temperature.
Features and Benefits of PVDF.
PVDF has some specific characteristics which are not found in other plastic raw materials. Here you have the advantages of PVDF injection molding explained:
- Excellent chemical resistance to a variety of aggressive fluids and solvents.
- Smooth, anti-fouling surfaces.
- Good permeation resistance.
- Injection molding grade.
- Excellent strength and dimensional stability.
- Good color stability.
Applications of PVDF
-
Chemical plant engineering with higher mechanical stress
-
Food and pharmaceutical industries with higher temperatures and mechanical loadings
-
Valves
-
Filter plates
-
Fittings
-
Pipelines
-
Coil bodies
Injection molding of plastic products.
We use steel molds to do the injection molding of plastic products. A mold is a one-time investment. In addition, it allows you to produce simple as well as complex plastic parts in an fast and economic way. The life time of a steel mold varies from 100 000 cycles to 300 000 cycles for a standard mold. However, it can go up to more than 1000 000 cycles for expensive molds. This lifetime is depending the type of steel, hardened or not, and the type of plastic used in the mold. Glass fiber filled plastics reduce the lifetime of a mold, for example.
Production time: how long does it need to produce a mold?
Our mold division needs an average production time of 35 working days to finish a mold. We do the mold test once the mold production is finished. It is possible dough that the mold needs adjustment. At last, we apply the surface texture or polishing after the plastic parts are accepted by our quality department. It is our standard procedure to ship final samples to the customers for acceptance. The production of series starts once the samples are accepted. We count about 20 days for the total process. Therefore, the production of each order is carefully scheduled in our production planning. Our procurement department will buy raw material in case there is no stock. With one mold we do an average of 1500 to 2000 cycles per day. Parts are checked after injection molding. We will remove burrs and pack the goods. Ready for shipping.
The number of cavities.
Injection molding of plastic parts is a very efficient production method. Especially when we can produce large quantities. The mold below has 12 cavities. This means we can produce 12 parts for each mold cycle. The result is a far cheaper unit cost per part. The mold, however, is more expensive. Nevertheless you will win the extra cost back in the total production cost of the plastic parts.
How does the injection molding process work?
Injection molding of plastic is an industrial process. Molten plastic is injected with high pressure into a mold. The mold is closed with a big force and remains closed during a certain time. The cycle time is depending on a number of factors such as plastic volume, wall thickness and type of plastic. A good design will reduce the cycle time.
There are 3 parameters to setup an injection molding machine :
- Pressure.
- Temperature.
- Time.
Each type as well as each different product needs different parameters. In addition the shrinkage of each plastic type is different. The cavities in the mold are larger than the final part. The reason is this shrinkage. A part will shrink once it is ejected from the mold. A part made of POM can shrink up to 20%. Products with a too big wall thickness can shrink even days later. Again, it is important to design a plastic part in a correct way.
Which kind of plastic ? Raw material
The choice of raw material for injection molding depends on the use of the final product and the desired properties. Obviously, there is a price difference between different types of plastic. For cheaper plastic products, where the finish and looks are less important, we mostly use PP (Polypropylene). To clarify, this is a strong material with good chemical resistance. We use it for outdoor furniture as well as toys. However, PP is not suitable for gluing and printing. We need to do a surface treatment first.
For enclosures of electronic devices, we use plastic injection molding of ABS of PC-ABS. This because of its robust properties, temperature resistance and surface finish. Polycarbonate injection molding or PC-ABS is more rigid and impact resistant. Usually, we make strong (tough) parts and moving parts of PA66 and POM. (these materials are also suitable for machining). Injection molding of PVDF as a technical plastic. Used for couplings and can resist higher temperature.
In our injection molding department we have 9 injection molding machines up to 560 Tons. For smaller parts and over-moldings, we use vertical injection machines from 25 to 45 Tons. Our factory is well organized and flexible. We are ISO9001:2015 certified as well as RoHS and REACH. Other certification and analysis of materials are possible via SGS. Injection molding of PVDF products by Davantech : your parts faster, cheaper and at higher quality!