CNC machining is a manufacturing process that uses computerized controls and machine tools to remove layers of material from a workpiece and produce a custom-designed part. More specific, the term CNC stands for computer numerical control. In other words, a computer program instructs the machine how to perform the machining operations. Therefore, this fabrication process can be used for a wide range of materials, such as metals, plastics, wood, glass, foam, and composites, and for various industries that require high precision and accuracy, such as aerospace, telecommunications, medical, and automotive.
CNC machining is a subtractive process, which means that it creates the desired shape by removing material from the workpiece. To clarify, this is different from additive processes, such as 3D printing, which create the shape by adding material layer by layer, or formative processes, such as injection molding, which deform and displace the material into the shape.

CNC Machining Explained
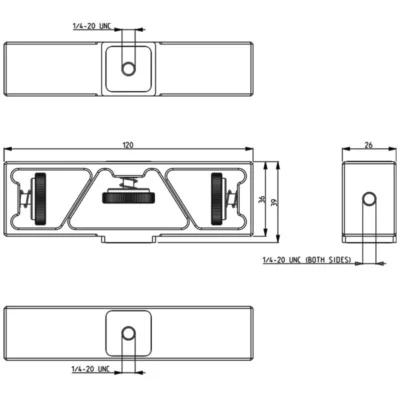
1. Designing the Workpiece in CAD Software
The process of obtaining a workpiece via CNC machining begins with the creation of a 3D digital model using Computer-Aided Design (CAD) software. This model serves as the blueprint for machining.
- CAD Software: Software like SolidWorks, AutoCAD, or Fusion 360 is commonly used. The model includes dimensions, features, and other specifications like holes, pockets, or slots.
- Considerations: The design must account for material removal, tolerances, and the machine’s limitations (like the axis of movement). The complexity of the part influences the type of CNC machine required and its operation parameters.
2. Selecting the Material for the Workpiece
The choice of material for the workpiece is critical. Different materials have unique properties like hardness, machinability, thermal conductivity, and corrosion resistance.
- Common Materials:
- Metals: Aluminum, steel, titanium, brass.
- Plastics: ABS, polycarbonate, nylon.
- Wood: Plywood, MDF.
- Composites: Carbon fiber, fiberglass.
- Factors in Choosing a Material:
- Strength and Durability: Metals like steel or titanium are used for heavy-duty parts.
- Cost: Aluminum is cheaper and lighter but may not have the durability of steel.
- Machinability: Some materials, like aluminum, are easier to machine than others, such as stainless steel.
3. Converting the Design to G-code Using CAM Software
After designing the workpiece in CAD, the next step is to convert this digital model into G-code using Computer-Aided Manufacturing (CAM) software. This G-code is what the CNC machine reads to perform the machining operations.
- CAM Software: CAM software like Mastercam or Fusion 360 generates G-code that includes detailed instructions for the CNC machine, such as:
- Tool paths.
- Spindle speeds.
- Feed rates.
- Cutting depths.
- Simulating the Process: Many CAM software programs allow you to simulate the machining process to detect any potential errors before actual production begins. This ensures the tool path will not lead to collisions or material wastage.
4. Preparing the CNC Machine and Setting Up the Workpiece
Once the G-code is ready, the CNC machine is set up to begin machining the workpiece.
CNC Machine Setup
- Choosing the Right CNC Machine: Depending on the workpiece design, you might use different types of machines:
- CNC Mills: For parts requiring multi-axis movement and milling operations.
- CNC Lathes: For cylindrical parts.
- CNC Routers: For cutting softer materials like wood or plastics.
- Tool Selection: Tools such as end mills, drills, and lathes are chosen based on the material and machining operations (e.g., cutting, drilling, or shaping). Tooling options vary in size, geometry, and material (e.g., carbide, high-speed steel).
Workpiece Setup
- Clamping or Fixturing: The material (workpiece) must be secured tightly to the machine’s table using vices, clamps, or custom fixtures. This ensures that the workpiece doesn’t move during the machining process, which would result in inaccuracies.
- Workpiece Zeroing: Before starting, the operator establishes a zero point (also called datum point) on the workpiece. This is where the CNC machine starts its operation. Accurate zeroing ensures that the machine performs all cuts in the correct positions relative to the design.
5. Executing the CNC Machining Process
With the machine and workpiece prepared, the CNC machining process can now begin. The machine follows the G-code instructions to shape the raw material into the desired workpiece.
- Machining Operations: The CNC machine performs a variety of operations, including:
- Cutting: Removing material using rotating cutting tools.
- Milling: Shaping the material with multi-axis movements.
- Drilling: Creating holes with specific depths and diameters.
- Turning: Rotating the workpiece on a lathe while a tool cuts material.
- Multi-Step Operations: Often, the machining process will be broken down into multiple steps. The machine may change tools automatically (in machines with tool changers) to perform operations like roughing (removing large amounts of material) followed by finishing (final, precise cuts for surface smoothness).
Types of CNC Machining Operations
- Roughing: This process involves the removal of large amounts of material quickly, typically with lower precision. It creates the general shape of the workpiece.
- Finishing: After roughing, finishing operations involve more precise and slower cuts, ensuring that the workpiece meets exact dimensions and surface finish requirements.
- Multi-Axis Machining: CNC machines with multiple axes (e.g., 3-axis, 4-axis, or 5-axis machines) can create complex shapes by rotating and moving the workpiece in different directions.
6. Post-Machining Processes and Inspection
After the CNC machining is complete, several post-machining processes may be necessary to finalize the workpiece.
Deburring
Machining processes often leave small sharp edges, burrs, or rough spots on the workpiece. These imperfections can be removed manually using deburring tools or through automated processes.
Surface Finishing
In some cases, additional finishing processes like polishing, anodizing, or coating may be applied to enhance the workpiece’s surface properties, appearance, or corrosion resistance.
Inspection and Quality Control
To ensure that the final workpiece meets design specifications, it must undergo thorough inspection. This may involve:
- Dimensional Inspection: Using calipers, micrometers, or coordinate measuring machines (CMM) to verify that all dimensions match the design tolerances.
- Surface Finish Inspection: Ensuring the surface meets roughness and smoothness requirements, often measured in microns.
7. Final Delivery or Assembly
Once the workpiece passes inspection, it can either be sent directly to the customer, used in assembly, or stored for future use. If part of a larger product, the workpiece will be integrated into the final assembly.
Advantages of CNC Machining
CNC machining has several advantages over other manufacturing processes, such as:
- There is the ability to produce complex shapes and geometries that are difficult or impossible to achieve with manual machining or other methods.
- High accuracy and repeatability, as the machine follows the exact instructions of the computer program without human error or variation.
- Production of parts with smooth surface finishes and tight tolerances, which are important for the functionality and aesthetics of the product.
- It is a cost-effective process for low to medium volume production runs, as it reduces the need for manual labor, tooling changes, and waste material.
The Difference between Milling and Turning
1. Basic Operational Difference
- CNC Milling: In CNC milling, the cutting tool rotates, and the workpiece remains stationary (though it may move along different axes depending on the machine). The rotating tool moves along various axes to remove material from the stationary workpiece. CNC milling is ideal for creating complex shapes, slots, holes, and contours in a workpiece.
- CNC Turning: In CNC turning, the workpiece rotates while a stationary cutting tool removes material from it. This process is used mainly for cylindrical parts, where the material is rotated at high speeds on a lathe, and the cutting tool shaves off the material to create the desired shape.
2. Machine Used
- CNC Milling Machine: A milling machine, often with a multi-axis setup (commonly 3-axis or 5-axis machines), where the spindle holds the cutting tool, and the table holds the workpiece. The table may move in various directions to enable complex cuts.
- CNC Lathe (Turning Machine): A CNC lathe or turning center, where the workpiece is held in a chuck or between centers and rotated at high speed. The cutting tool remains fixed and removes material from the rotating workpiece.
3. Types of Parts Produced
- CNC Milling: This process is versatile and is used for parts with complex geometries that have flat surfaces, curves, and intricate details. It can produce:
- Complex shapes with intricate details.
- Non-cylindrical parts (e.g., blocks, enclosures).
- Parts with multiple surfaces or angles, such as brackets, gears, and engine parts.
- CNC Turning: Turning is typically used for parts that are cylindrical or round. The parts produced are often:
- Shafts, bushings, and cylindrical components.
- Conical shapes or surfaces with various diameters.
- Threaded parts, such as screws or bolts.
4. Movement and Axes
- CNC Milling: Milling machines usually operate in 3, 4, or 5 axes:
- 3-axis milling: Moves the tool along the X, Y, and Z axes to shape the workpiece.
- 4-axis milling: Adds rotational movement to the 3-axis setup, allowing the cutting tool to rotate around the workpiece.
- 5-axis milling: Allows the cutting tool to move in all directions and around two additional axes, enabling complex shapes with high precision.
- CNC Turning: Turning typically involves 2 axes (X and Z):
- Z-axis: Controls the length of the part by moving the cutting tool along the axis of rotation.
- X-axis: Controls the diameter of the part by moving the cutting tool perpendicular to the axis of rotation.
- Advanced CNC turning centers can include additional axes for milling operations, known as mill-turn centers.
Limitations of Milling and Turning
CNC machining also has some limitations and challenges, such as:
- CNC machining is expensive for high volume production runs, as it requires a high initial investment in machines, software, and maintenance.
- There is waste of material, as it removes a large amount of material from the workpiece that cannot be reused or recycled.
- Machines limit the size and shape of the workpiece and the machine tool, as some parts may be too large or complex to fit or be machined by the available equipment.
- External factors effect the machining process. More specific, temperature, humidity, vibration, and wear and tear of the machine components. As a result, this affects the quality and performance of the machining process.
Parts Made by the Machining Process
CNC machining produces a wide variety of parts for different applications and industries. Some examples are:
-
Aerospace parts:
Fabrication of complex and precise parts for aircrafts, rockets, satellites, and other aerospace vehicles. These parts include turbine blades, engine components, landing gear, wing flaps, and fuselage panels.
-
Medical parts:
Manufacturing intricate and accurate parts for medical devices, implants, instruments, and equipment. These parts include surgical tools, dental implants, orthopedic implants, prosthetics, and pacemakers.
-
Automotive parts:
Production of durable and functional parts for cars, trucks, motorcycles, and other vehicles. These parts include engine blocks, pistons, cylinders, gears, shafts, brake discs and suspension components.
-
Aerospace parts:
CNC machining creates complex and precise parts for aircrafts, rockets, satellites, and other aerospace vehicles. These parts include turbine blades, engine components, landing gear, wing flaps, and fuselage panels.
-
Medical parts:
We us CNC machining to produce intricate and accurate parts for medical devices, implants, instruments, and equipment. These parts include surgical tools, dental implants, orthopedic implants, prosthetics, and pacemakers.
-
Automotive parts:
CNC machining makes durable and functional parts for cars, trucks, motorcycles, and other vehicles. These parts include engine blocks, pistons, cylinders, gears, shafts, and
-
Electronics parts:
CNC machining produces small and complex parts for electronic devices, gadgets, and equipment. These parts include circuit boards, connectors, switches, buttons, and casings.
-
Industrial parts:
Milling and turning is suitable to make large and heavy parts for industrial machinery, equipment, and tools. These parts include shafts, bearings, bolts, flanges, and valves.
Conclusion
CNC machining is a manufacturing process that uses computerized controls and machine tools to remove material from a workpiece. This enables us to produce and custom-designed parts. More specific, the industry uses it for manufacturing a wide range of components that require high precision and accuracy. In addition, there are several advantages over other manufacturing processes. Some advantages are complexity, repeatability, surface finish, and cost-effectiveness for low to medium volume production runs. However, it also has some limitations and challenges, such as waste material, size and shape constraints, external factors, and high initial investment for high volume production runs.
There are many types of machinery that can perform different kinds of machining operations. Some of the most common types are milling and turning machines, drilling machines, and grinding machines. The manufacturing process produces a wide variety of parts for different applications and industries. Some examples are aerospace parts, medical parts, automotive parts, electronics parts, and industrial parts. In addition, CNC machining works with a wide range of materials, depending on the type of machine and the desired properties of the part. Some of the most common materials are metals, plastics, wood, and composites.